Honda Motor is embarking on the next phase of its manufacturing evolution in an unexpected location for the 75-year-old Japanese automaker: Ohio.
The company is finalizing over $1 billion in new investments in the state this year, an increase from the initially announced $700 million. These upgrades include the installation of six “giga presses”—a technology popularized by Tesla—and a new “cell” manufacturing system designed for assembling electric vehicle (EV) battery cases.
Honda’s emerging EV hub in Ohio, which includes a separate $3.5 billion battery plant, will serve as the flagship for the company’s global manufacturing strategy. Officials noted that the Marysville Auto Plant will be capable of producing traditional vehicles, hybrids, and EVs on a single assembly line.
“The Honda EV hub in Ohio is establishing the global standard for EV production for people, for technology and for processes,” said Mike Fischer, North American lead for Honda’s battery-electric vehicle projects. “As we expand EV production regionally and globally, this is the footprint and the characteristic performance that will be used.”
Typically, significant manufacturing shifts at Honda would first be introduced in Japan before being implemented in U.S. facilities and beyond, company officials said.
The Ohio investments were initially announced in October 2022 as part of the Biden administration’s push to strengthen domestic manufacturing. They remain critical amid potential tariff increases on imported goods, including automobiles, under President Donald Trump.
Honda produced more than 1 million vehicles at its five U.S. assembly plants in 2024, with approximately 64% sold domestically and the remainder exported. The company also operates one assembly plant in Mexico.
Once the upgrades are complete, Honda’s Marysville plant—located in central Ohio near Columbus—will have the capacity to produce roughly 220,000 vehicles annually. The 4-million-square-foot facility currently manufactures several Honda and Acura models, and later this year, it will begin producing the all-electric Acura RSX crossover, the company’s first EV to be built in-house.
The Japanese automaker was slower than some competitors in investing in EVs. Currently, its two all-electric crossovers—the Honda Prologue and Acura ZDX—are built by General Motors in Mexico.
The new Acura crossover will be followed by the Honda 0 SUV and Honda 0 Saloon EV prototypes, which Honda unveiled at CES in Las Vegas last month.
The aluminum battery packs for Honda’s next-generation EVs will be manufactured at the company’s engine complex in Anna, Ohio—its largest engine facility worldwide. Since its inception in 1985 as a small rectangular building, the plant has expanded to over 2.8 million square feet.
“We’re establishing this large aluminum production technology for all Honda,” said Tim Stroh, EV battery case project leader. “The goal here is to roll that out to other products, other factors across the world.”
To produce battery packs and other EV components—and possibly engines in the future—Honda is installing six massive 6,000-ton high-pressure die cast machines.
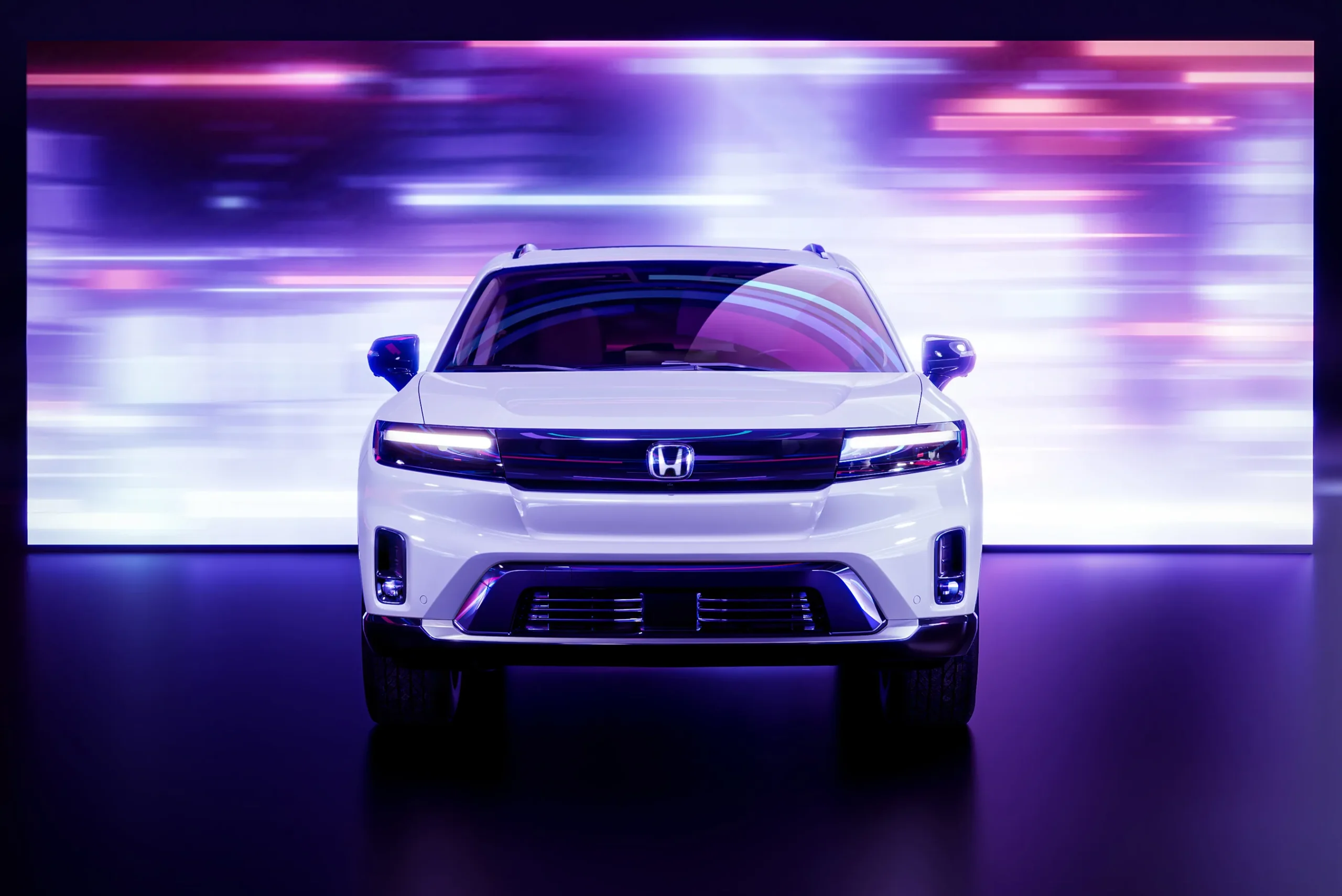
These machines will “megacast” or “gigacast” materials, similar to Tesla’s approach. Each of these machines is as large as a small house and applies extreme pressure to shape vehicle parts. In comparison, the largest presses Honda currently operates in Ohio generate 3,500 tons of pressure.
If executed effectively, gigacasting could significantly reduce per-unit manufacturing costs by eliminating the need to weld multiple body components, instead forming a single module, according to S&P Global Mobility.
Once cast, the battery packs will be transported from Anna to Marysville and other Honda facilities, where battery cells from Honda’s joint venture with LG Energy Solution will be integrated before the final EV assembly.
To streamline the battery integration process at Marysville, Honda is introducing nearly 60 flexible manufacturing “cells,” or zones, for battery assembly.
Unlike a traditional assembly line, where vehicles progress along a conveyor system, this new approach allows different tasks to take place in designated zones, ensuring that any slowdowns or issues do not disrupt overall production.
“This is considered the second founding for Honda,” said Bob Schwyn, senior vice president of Honda Development and Manufacturing of America. “We’re using the opportunity to reimagine our approach to manufacturing.”
Honda has referred to its shift to electric and fuel-cell vehicles as its “second founding.” Despite EV adoption in the U.S. progressing slower than anticipated, the automaker remains committed to its long-term goal of achieving zero environmental impact by 2050. This initiative focuses on three key areas: carbon neutrality, clean energy, and resource circulation.
That vision also includes selling only zero-emission vehicles by 2040—a target that many other automakers have recently delayed or abandoned.
Beyond expanding its EV capabilities, Honda’s more than $1 billion investment in its Ohio facilities includes implementing innovative manufacturing techniques to reduce emissions and waste. One such initiative involves using a specialized type of structural aluminum for battery packs, which can be fully recycled and reused.
“We’re using the opportunity to reimagine our approach to manufacturing and create new value in the area of environmental responsibility,” Schwyn said. “This includes strategies to recapture our products at end-of-life and then recycle or reuse 100% of the materials, especially finite materials for EV batteries, to essentially make new Hondas out of old Hondas.”